And finally on this last post, I’m putting a lid on it.
—
We raised the roof – with some winching and a little wincing (from my mother). But let’s get to making this roof beam.
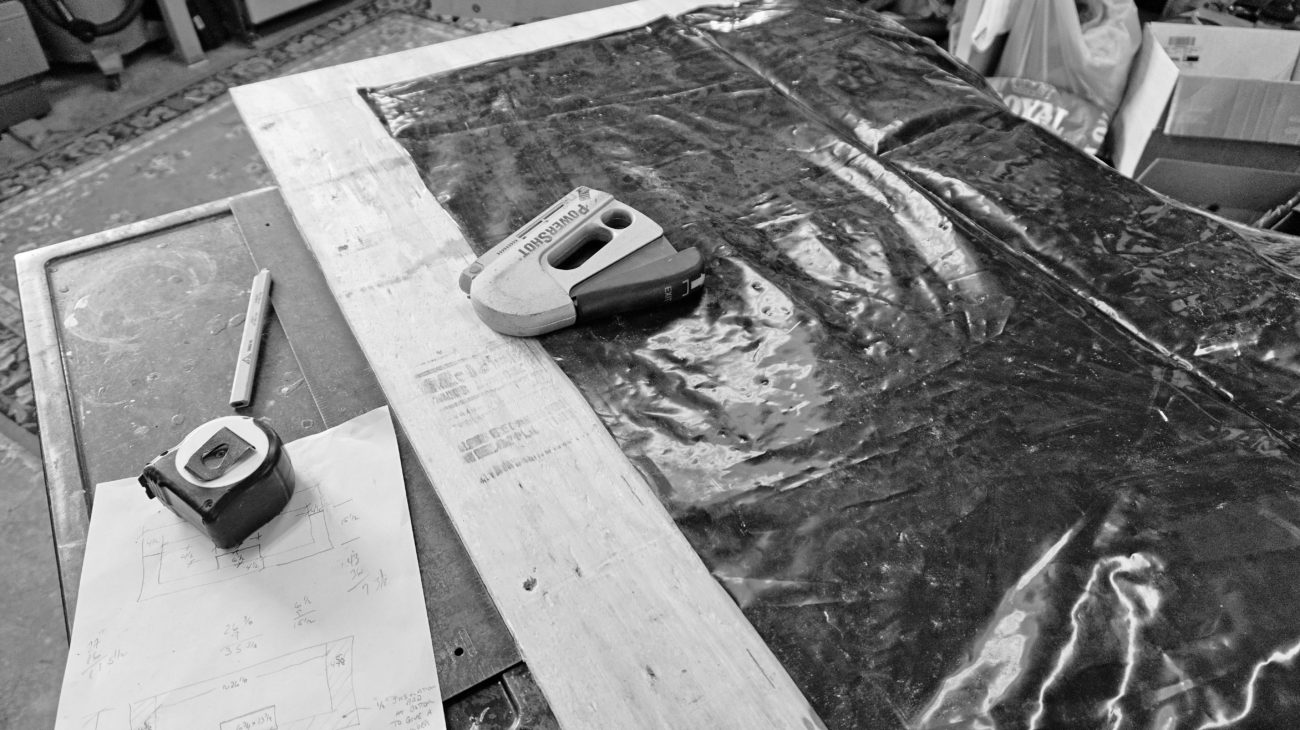
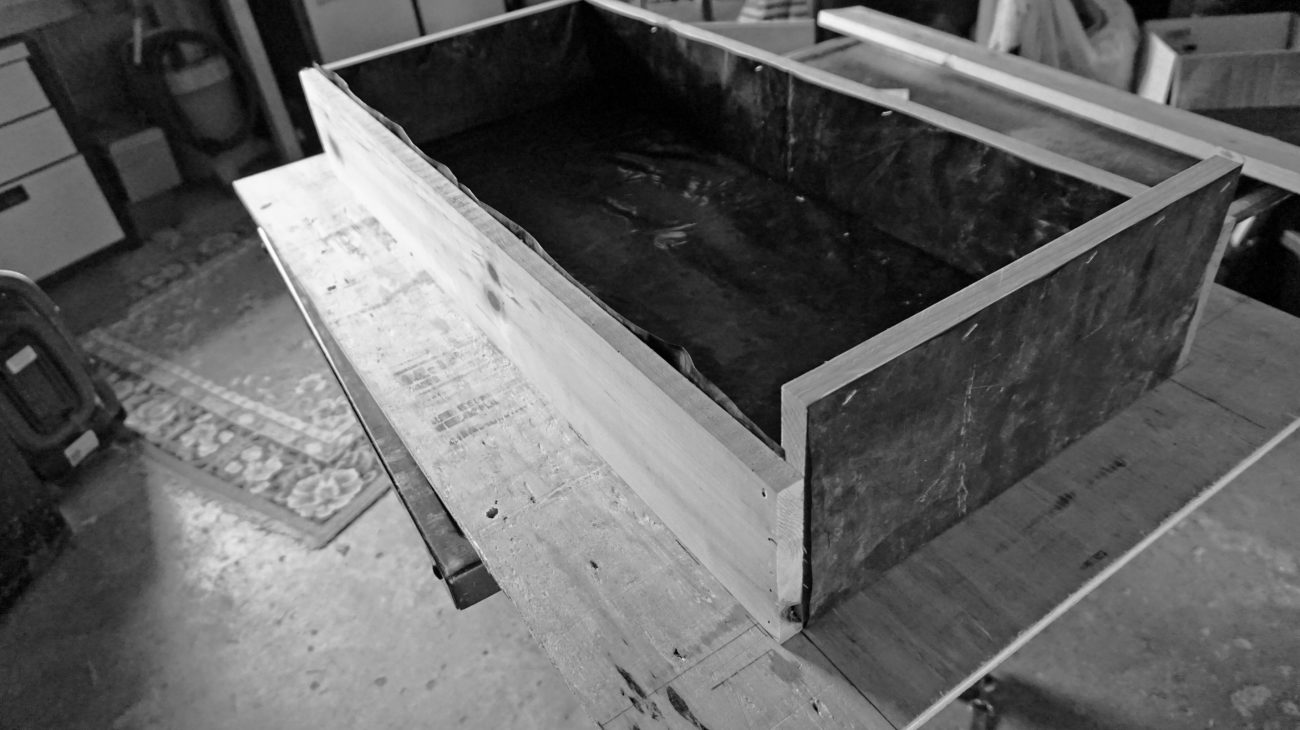
This is well for the top of the chimney box (to exhaust the heat).
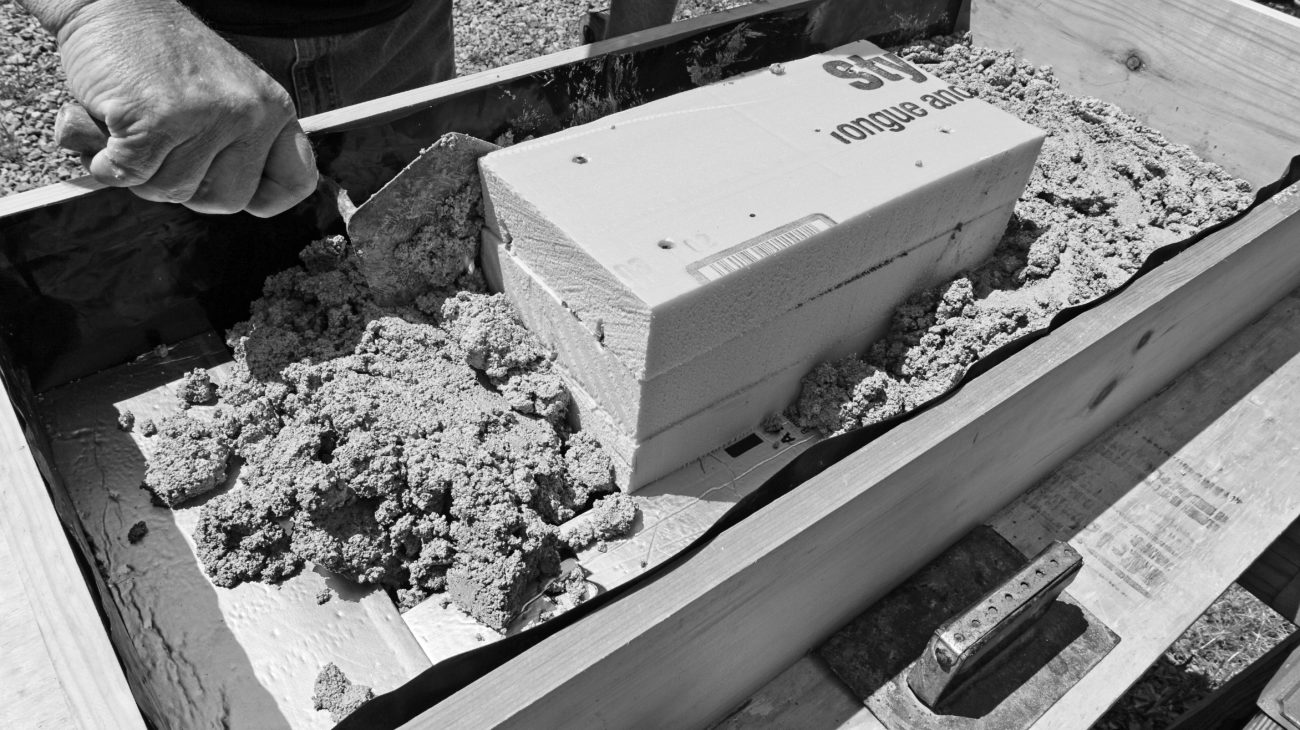
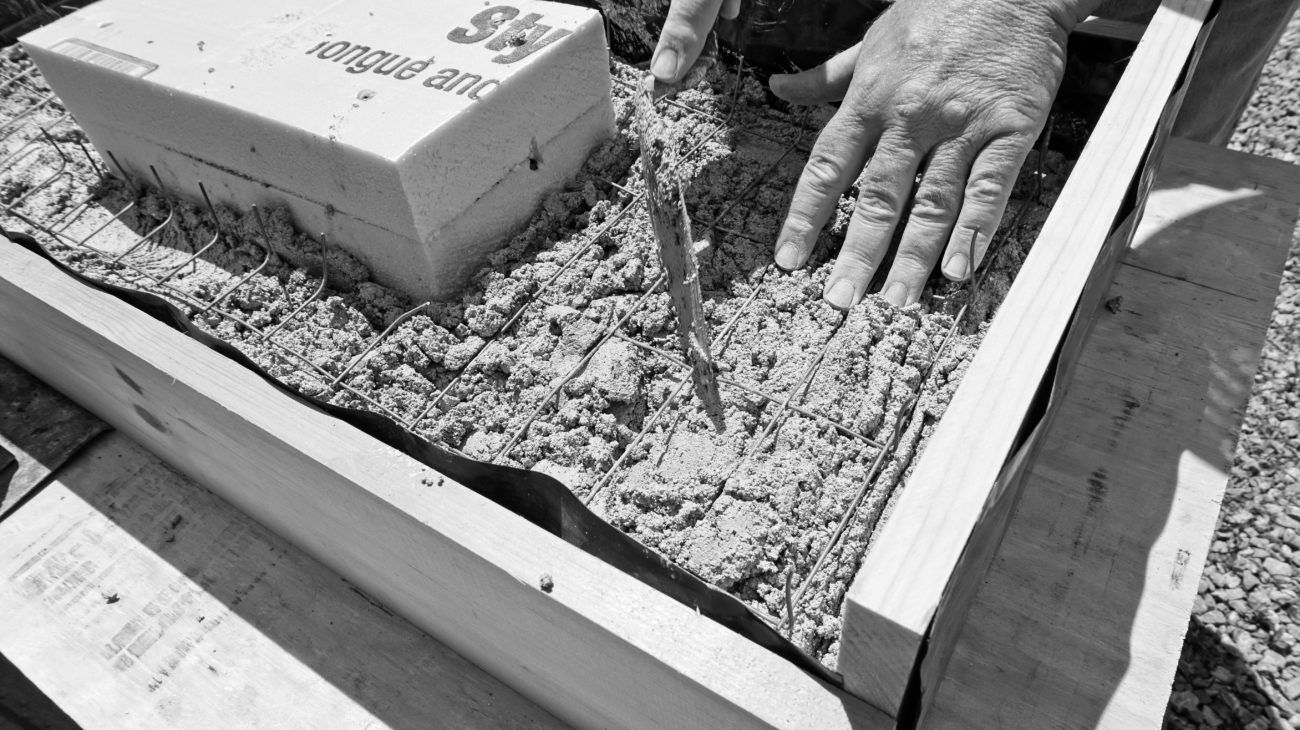
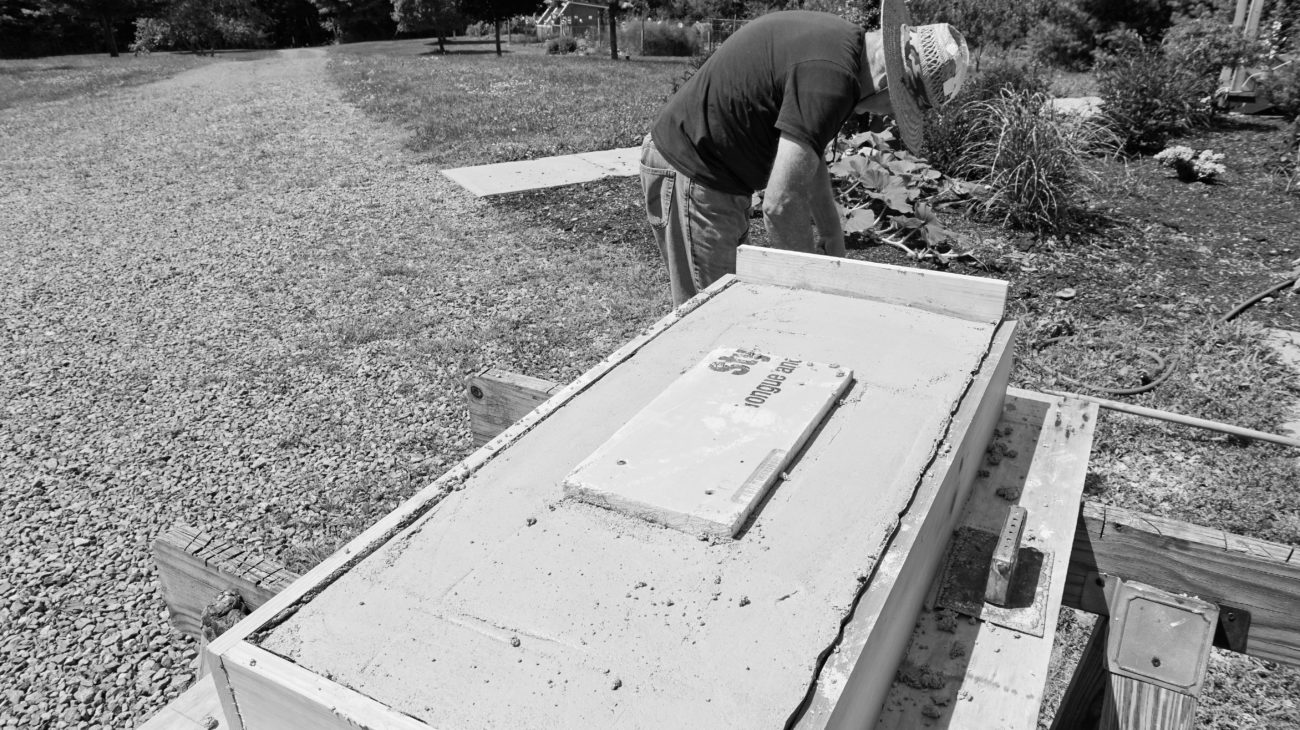
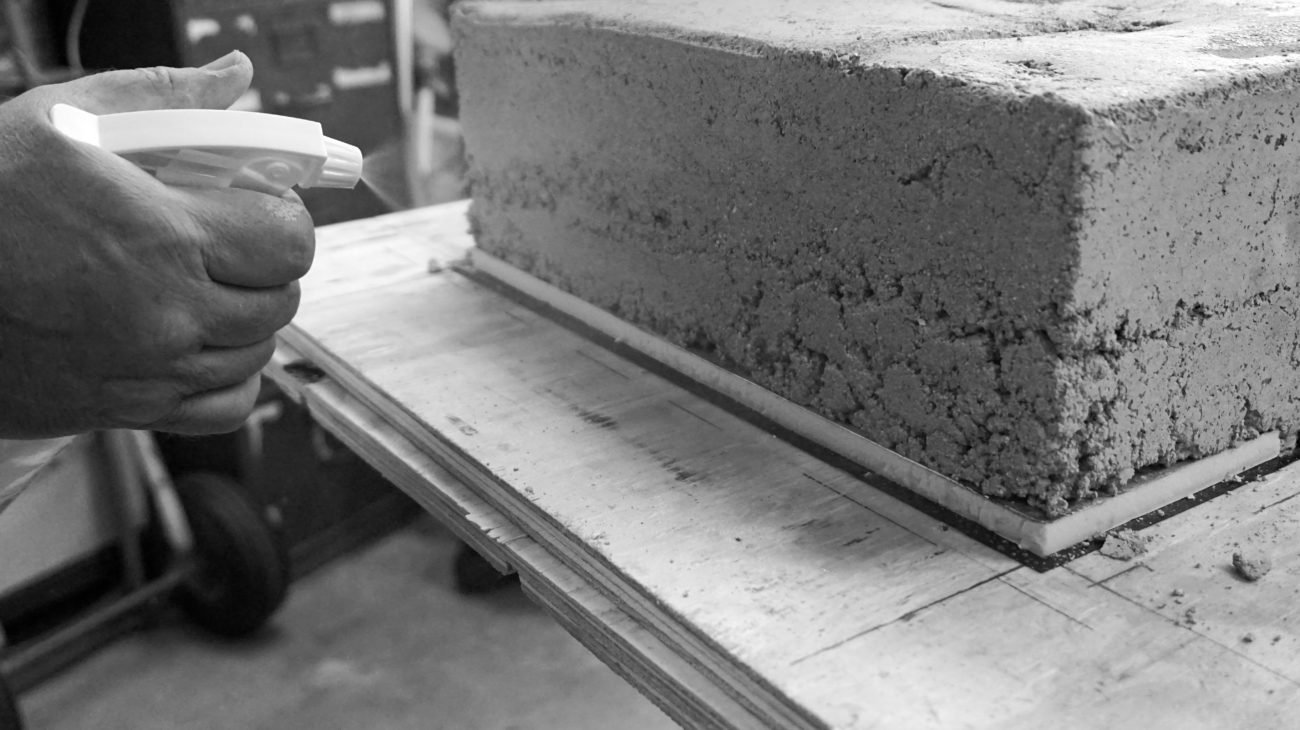
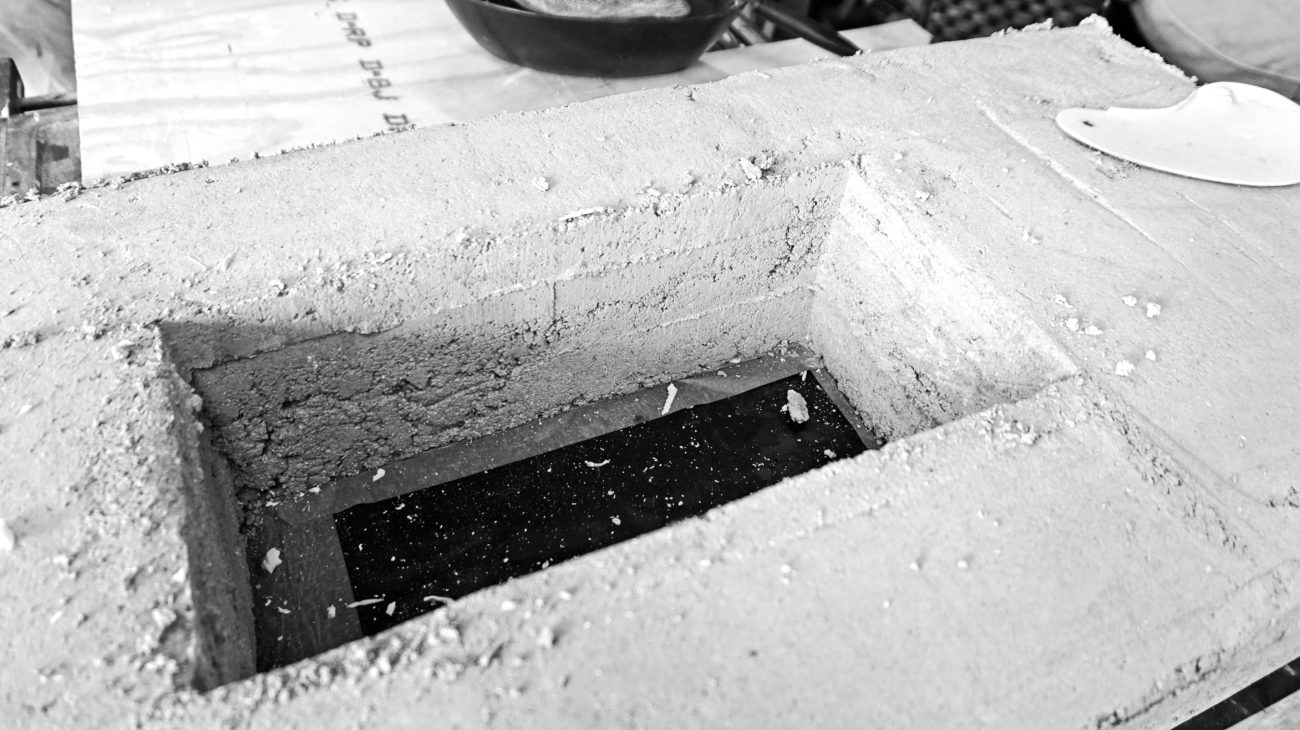
One week later (another Saturday) we popped that baby out of there. A little bit of cleanup of residual stuck insulation board but relatively clean.
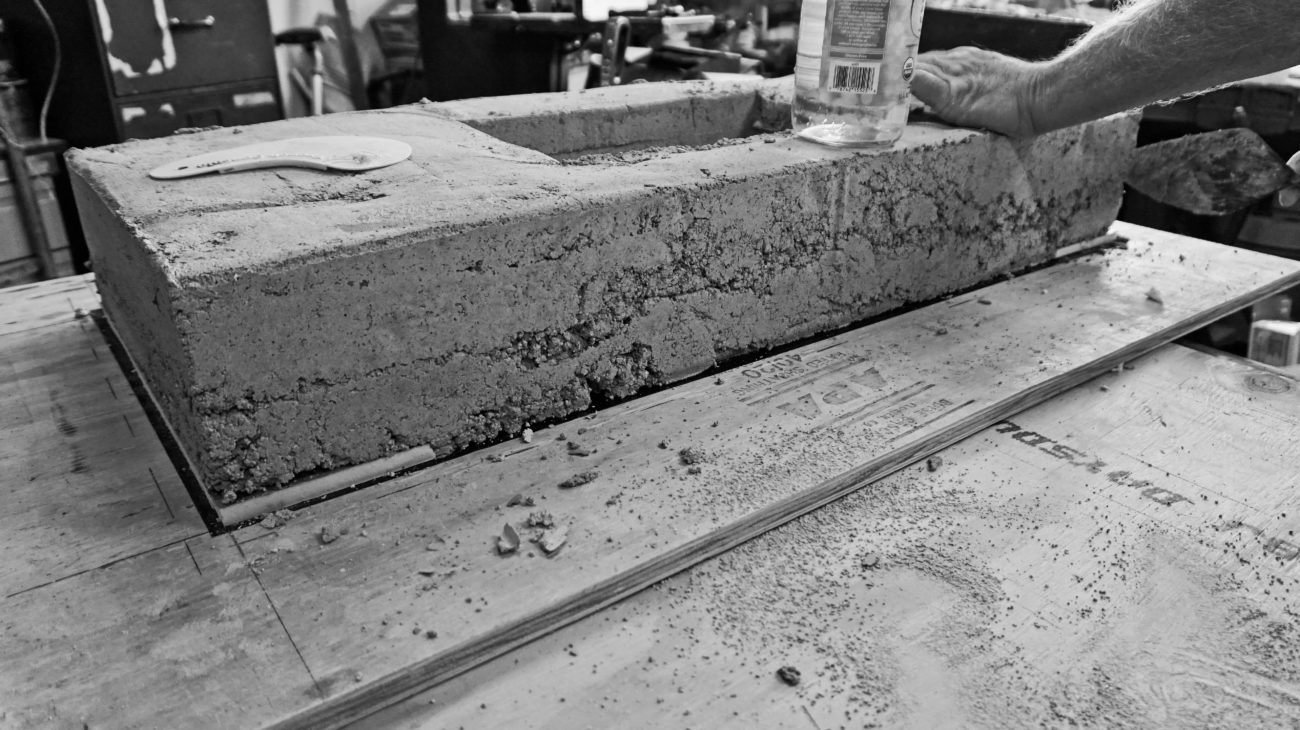
Slight detail finishing work, and surely that right-hand side where you can see less compression is probably on account of me not being girthy enough to push it down.
To compensate for some areas that weren’t compressed well enough, the sides were wet again and cement added to smooth it out. This created a clean edge so I’m not cutting myself as I’m reaching into the kiln with delicate pots.
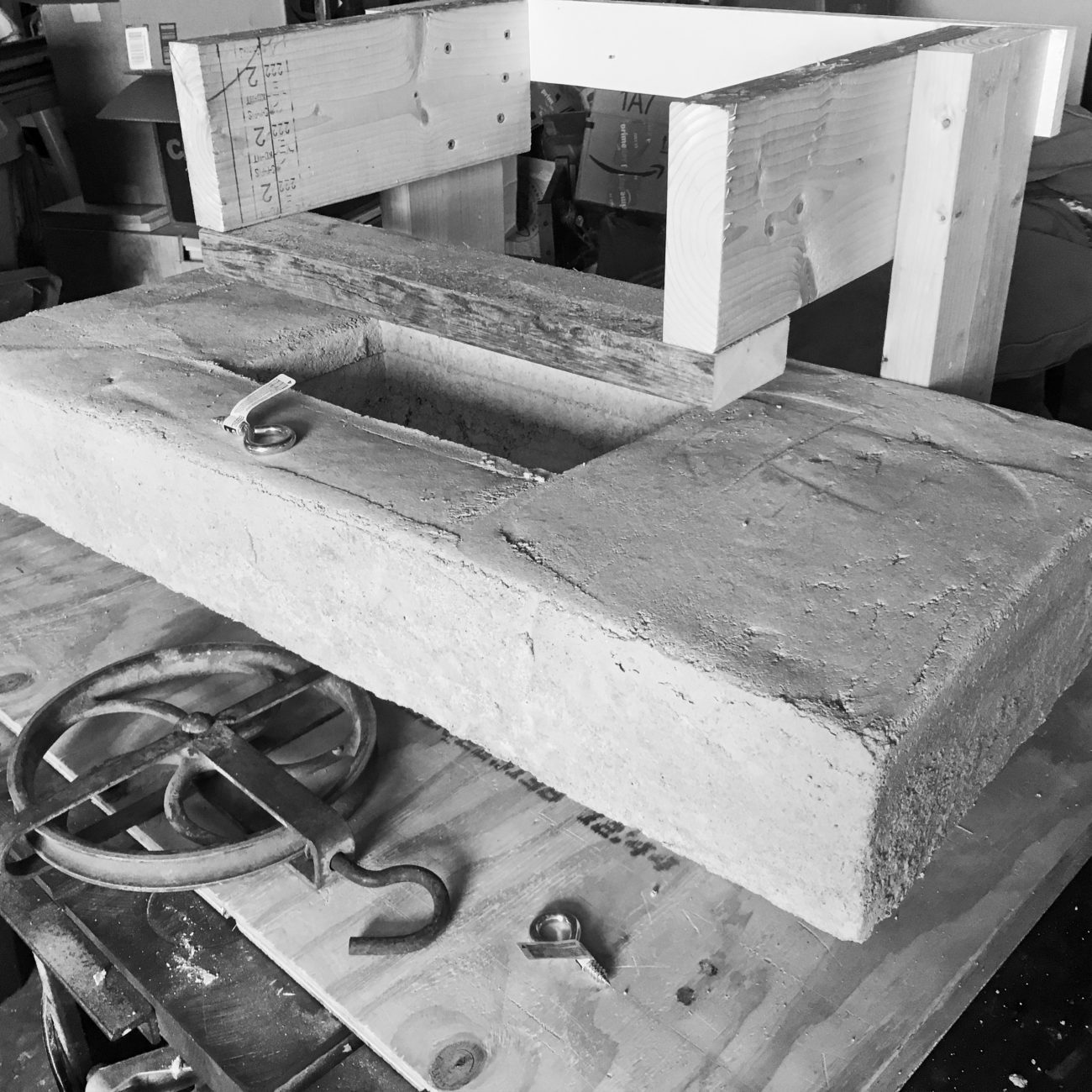
Five days later, the cement top was cured. A cradle was made to hold and lift the roof beam. The kiln is quite tall, and the caulk does set up enough that it was worth having it overhead and held and lowered evenly. It’s a heavy piece on its own.
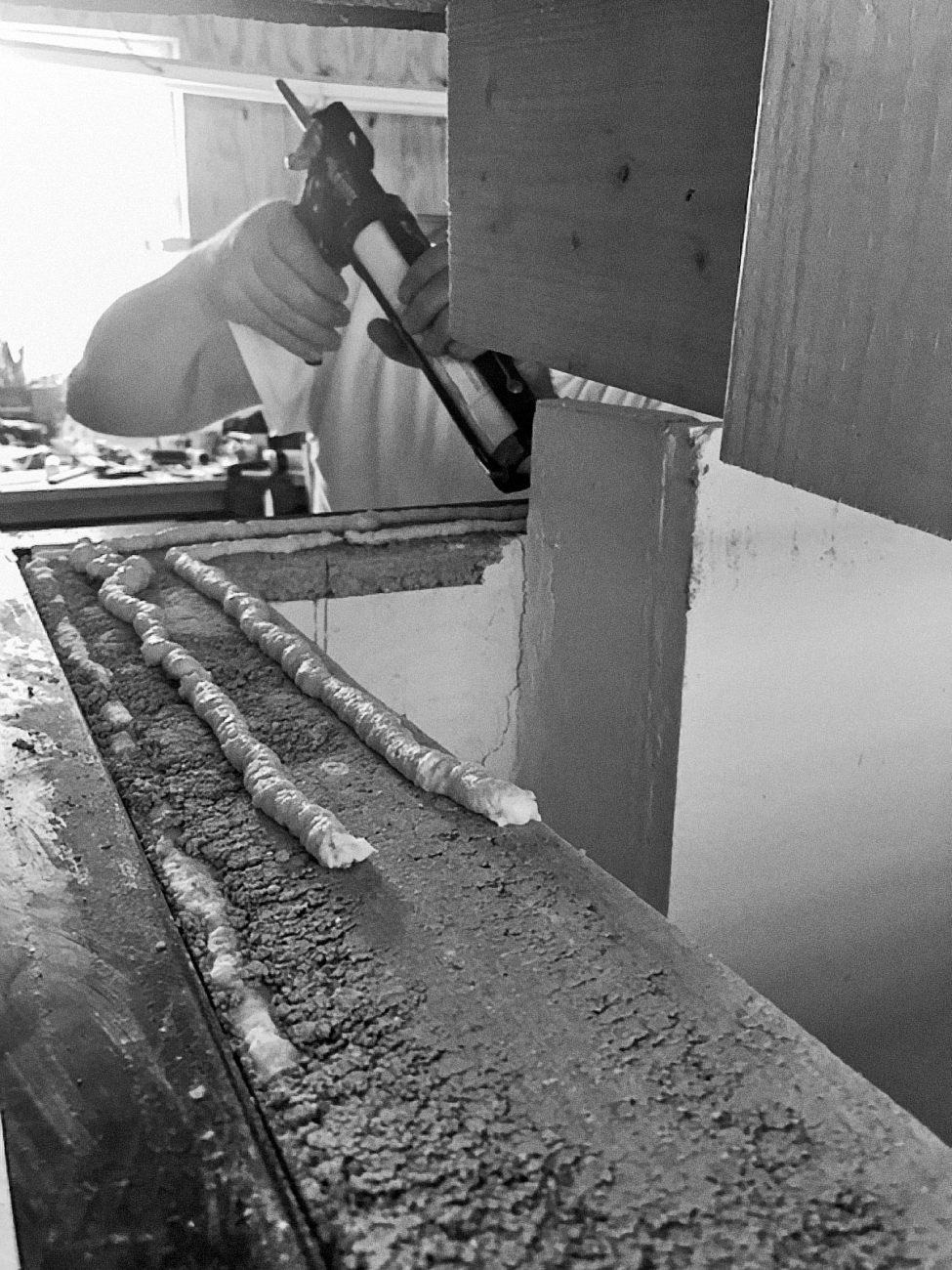
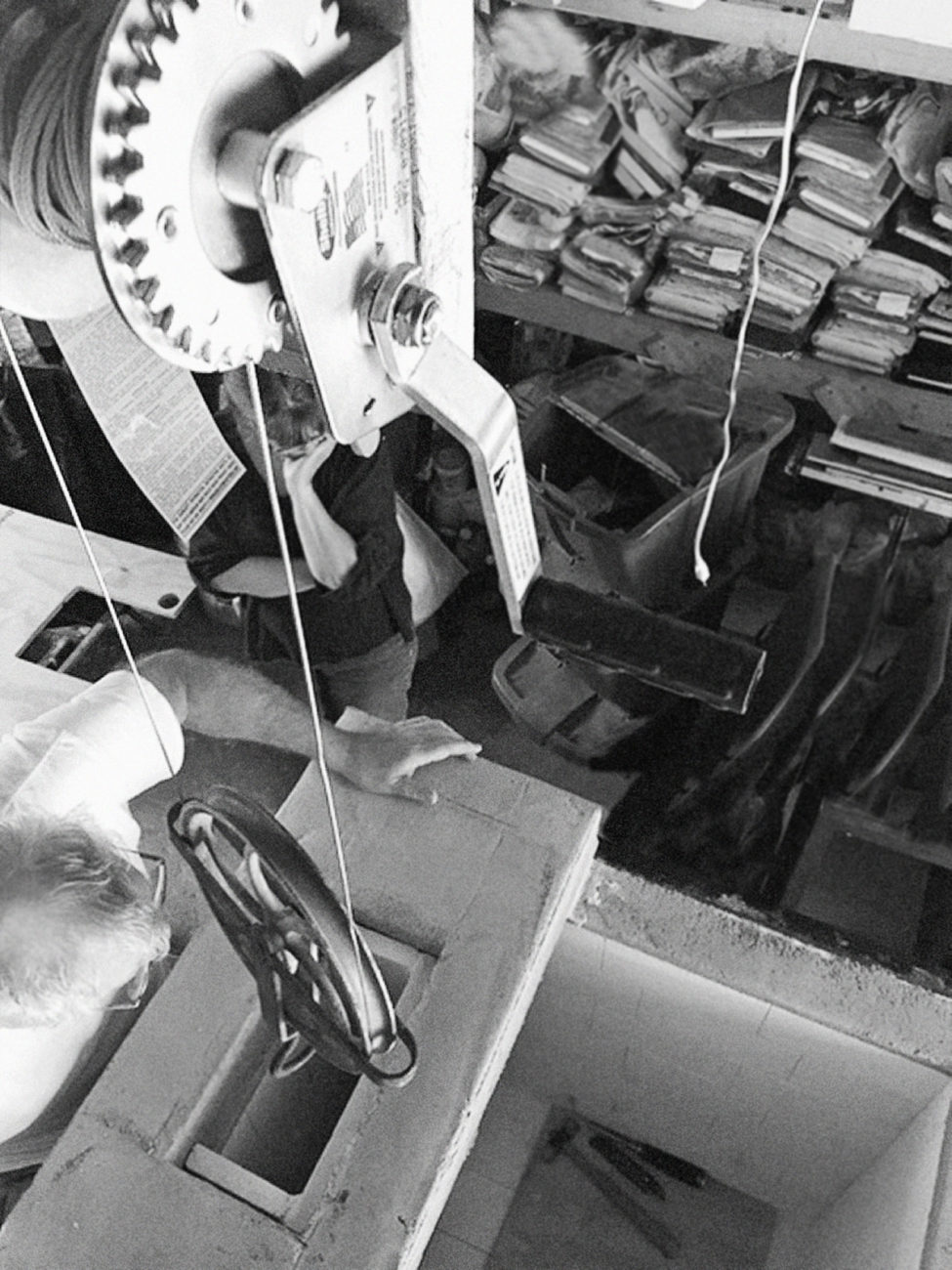
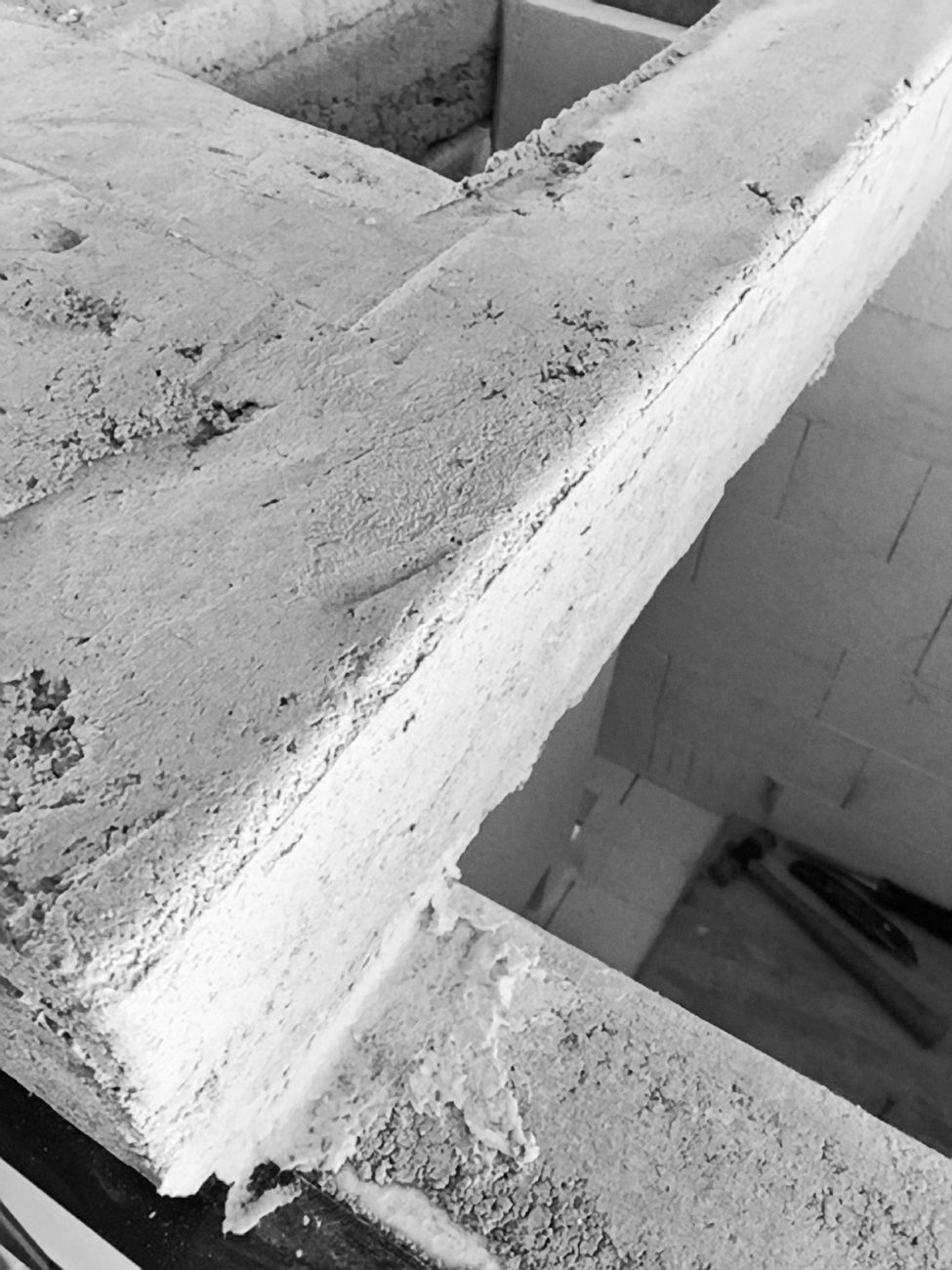
Without much fanfare, the kiln is done, albeit the lid that nests against the roof beam. That was made with the ceramic fiber while I returned to a freelance assignment in NYC and didn’t get to record that detail.
A peep hole will be made as well to view inside the kiln.
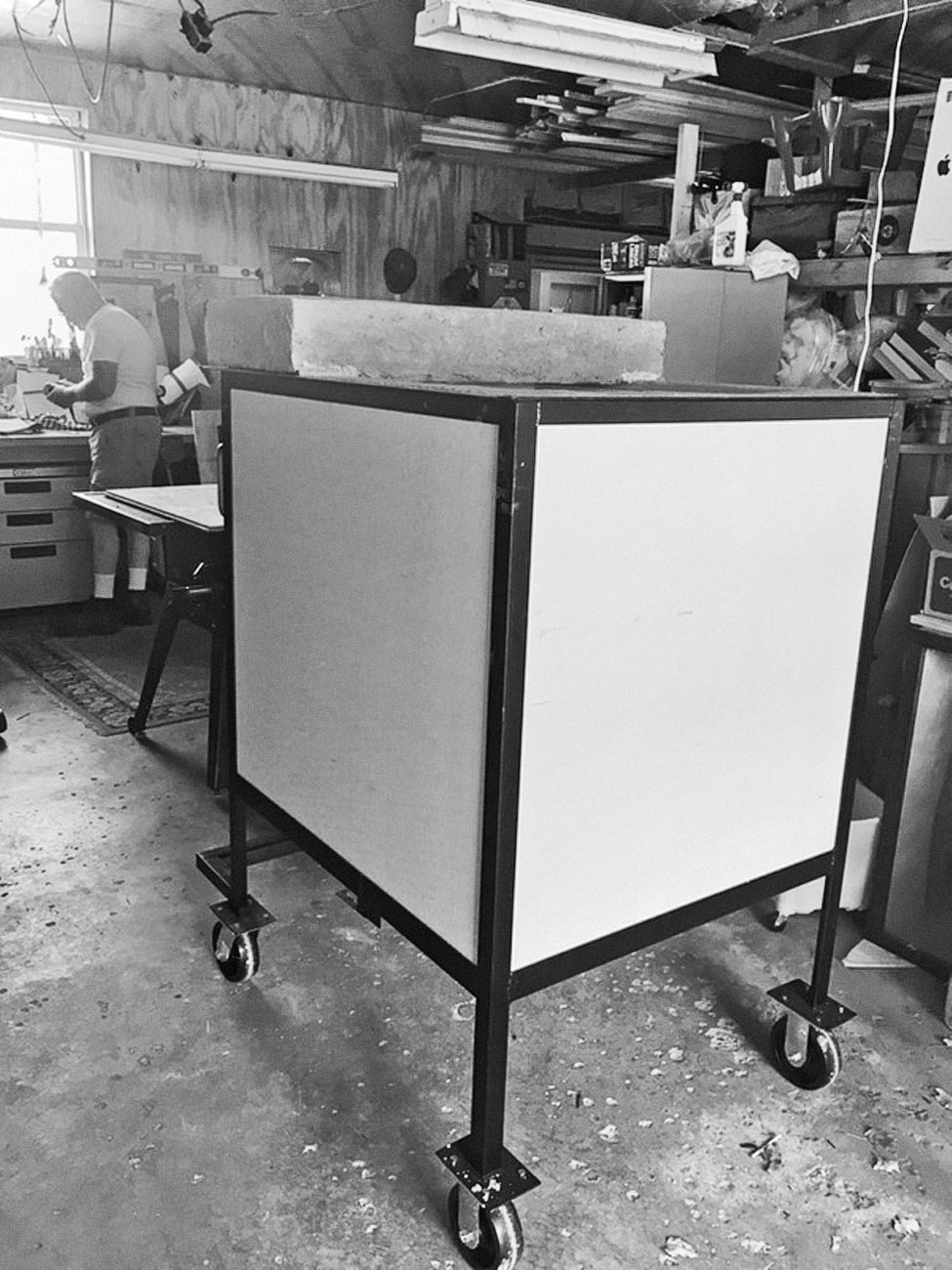
Testing the burners
Looking back, this day was as exciting as every other step. I love watching this as this is so typical of the exchanges between my parents.
My mom worried about everything going wrong, and my dad, cool and collected.
If you are just coming to this series of the gas #powerkiln and want to read through the build from the beginning, you can click below. I’m happy to answer what questions I can. Anything extremely technical I will do my best to get you the answers you need. Calculations such as the burners and your final design size is best discussed with Ward Burner. To compare refractory material you can look at Sheffield Pottery in Western Mass which was my closest supplier.
1 thought on “Put A Lid On It”
Pingback: MyBlog